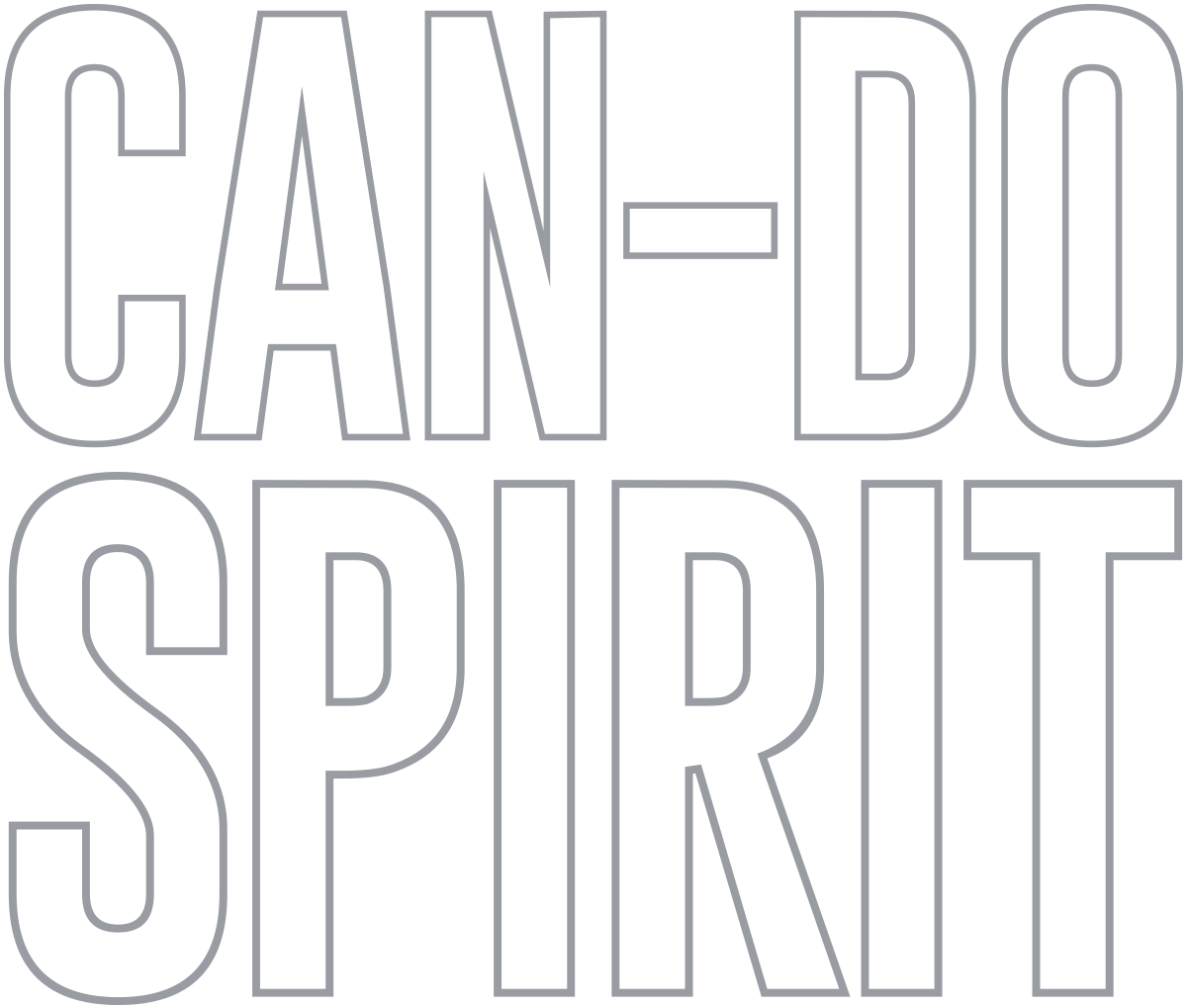
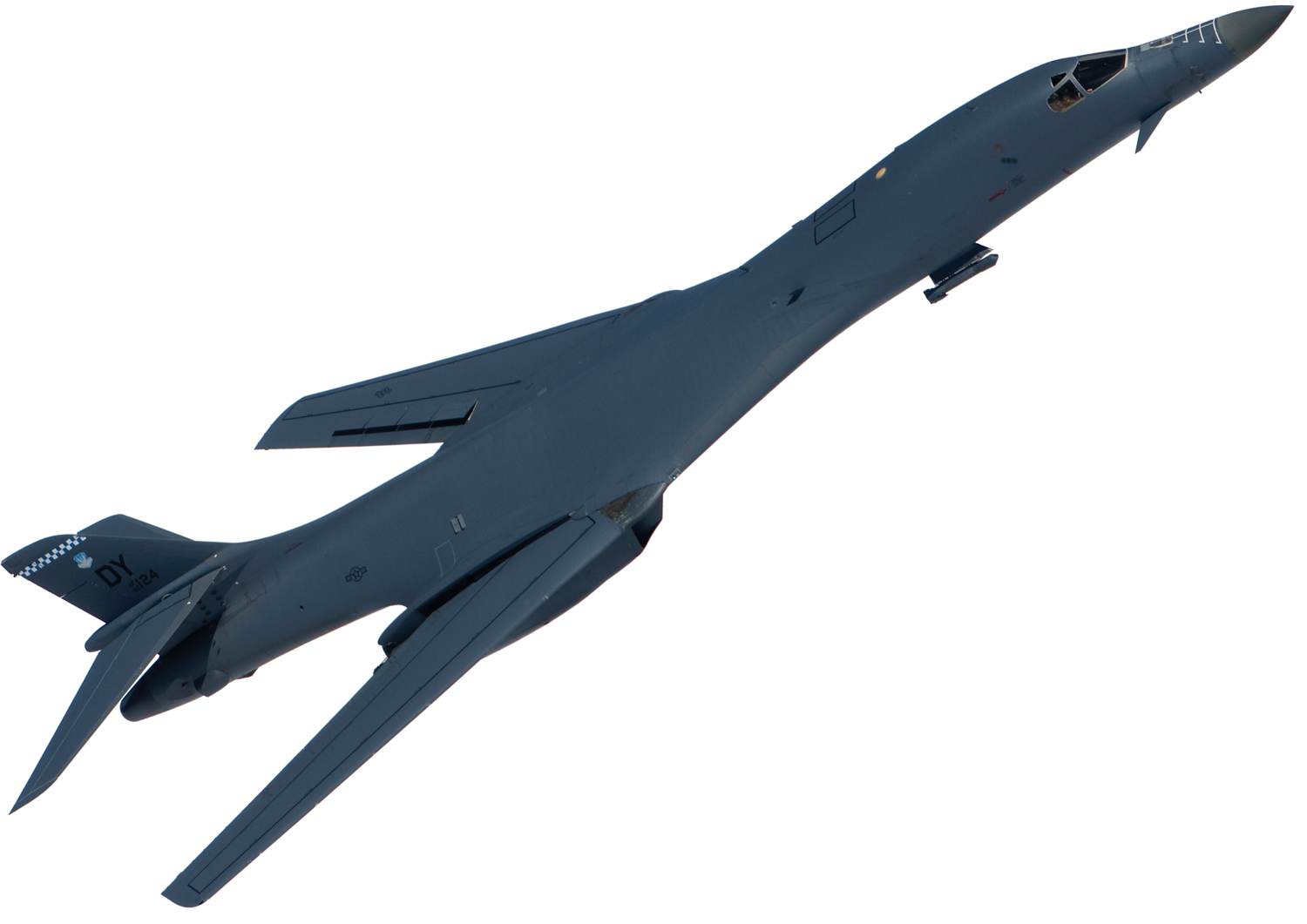
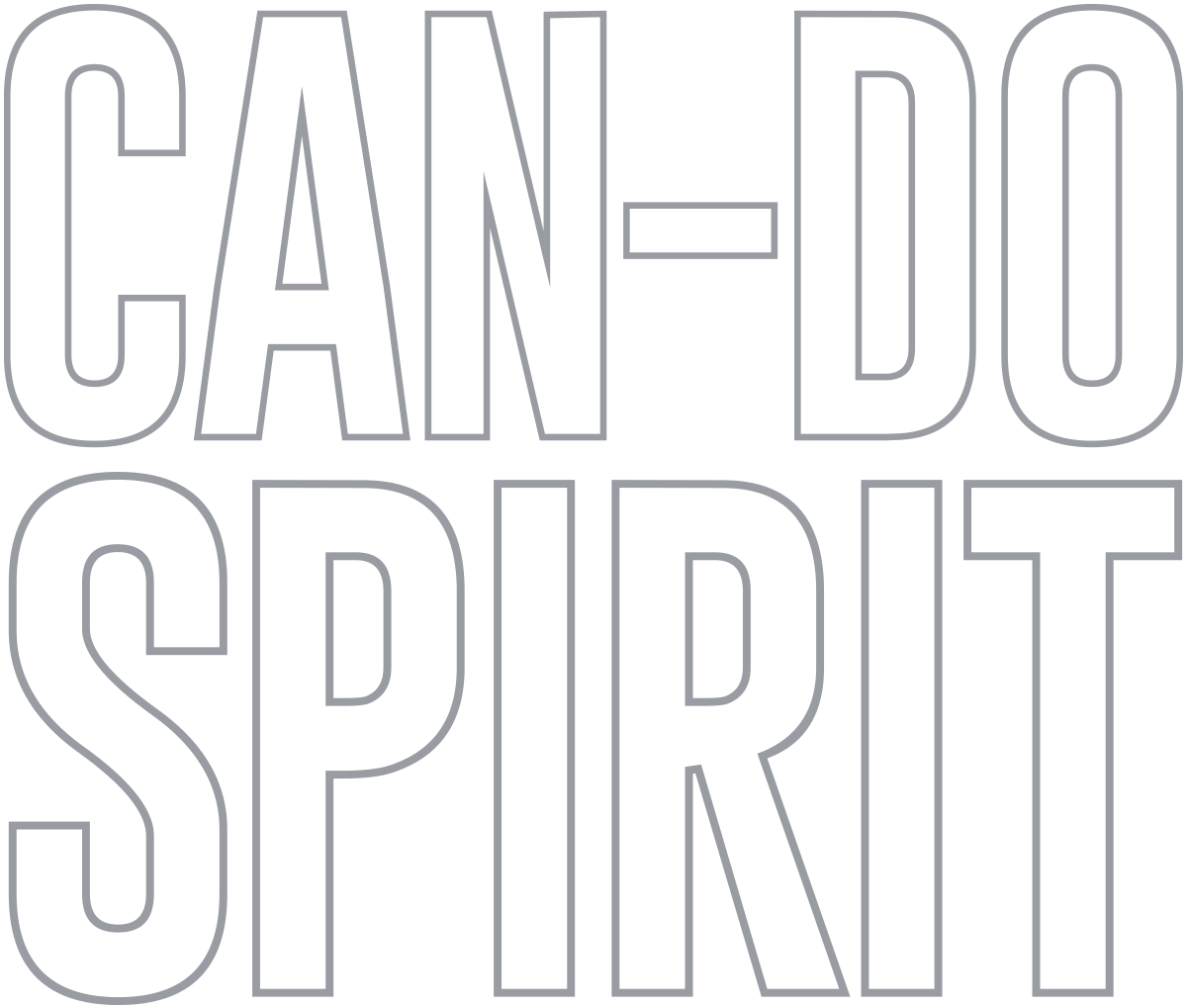
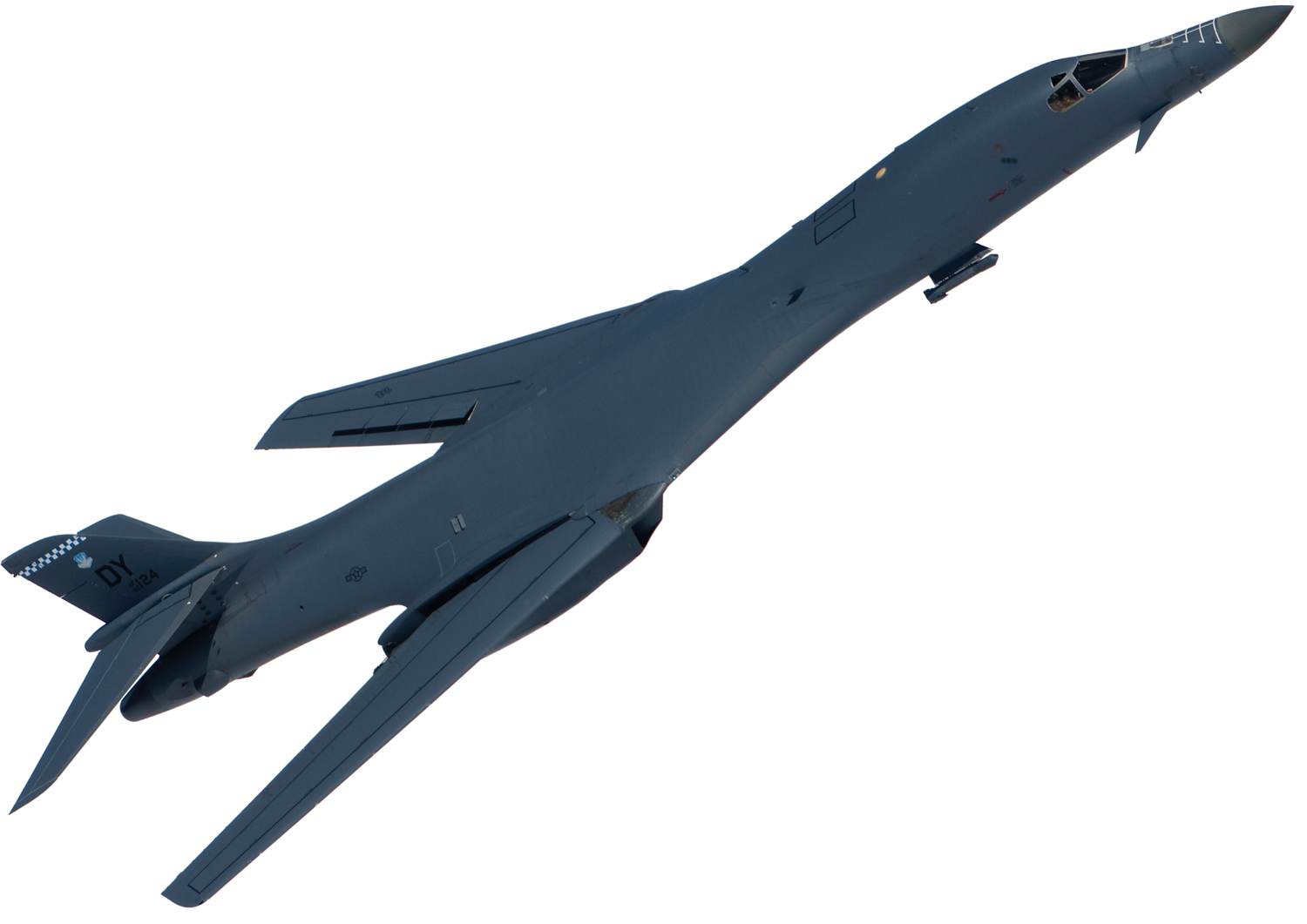
.S. citizens are largely trusting of our military, and for good reasons. Service members sacrifice to protect Americans and American interests at home and abroad. What we rarely think about is what it takes to keep the planes flying, in a timely fashion, and how innovative ground crews, technicians and others have to be to achieve that.
A vital tool in the arsenal is, of course, the Air Force Research Laboratory (AFRL), whose mission is to lead “the discovery, development and integration of warfighting technologies for air, space and cyberspace forces.” Let’s take a look at how that works in the real world.
During a single three-month period, the Air Force may have 10,000 requests for parts that received no bidder because the original manufacturer was out of business or it was not feasible for the supplier to produce needed parts.
The Air Force Research Laboratory has created a program called Maturation of Advanced Manufacturing for Low Cost Sustainment. Partnering with universities and the private sector, it uses advanced technologies to address the challenges of keeping aging aircraft flying safely. One Maturation team was tasked with reassembling an F-16 tail that had been shot full of holes and then disassembled. The tail could not be reconstructed due to the lack of needed tooling and technical data.


This effort was able to reclaim an Air Force asset worth between $600,000 and $1 million and support fleet readiness.
“One of the most difficult things to overcome in the F-22 community, because of the small fleet size, is the availability of additional parts to support the aircraft,” says Robert Lewin, 574th AMXS director.
The use of 3D printing gives technicians the ability to acquire replacement parts on short notice without minimum order quantities. This not only saves taxpayer dollars but also reduces the time the aircraft is in maintenance.
The 3D-printed bracket, made from titanium powder, will not corrode. Produced using a powder bed fusion process that employs a laser to build the part layer by layer, a new bracket can be ordered and delivered to a squadron depot for installation as quickly as three days.
The titanium powder part replaces a corrosion-prone aluminum component in the kick panel assembly of the cockpit that is replaced 80 percent of the time during maintenance.
The new titanium bracket is only the first of many metallic additive manufactured parts planned through public-private partnerships. There are at least five more metallic 3D printed parts planned for validation just on the F-22.
“Once we get to the more complicated parts, the result could be a 60- to 70-day reduction in flow time for aircraft to be here for maintenance,” Lewin predicts.
Photo: USAF/Ethan Morgan
In its quest to get repairs made and keep the fleet healthy for 20 more years, Tinker Air Force Base teamed up with the 76th Aircraft Maintenance Group (AMXG) to create a dedicated repair line “just to repair B-1 structural issues,” Barnes says. The first B-1 to go through the line arrived in October.
The facility will now manage seven urgent repairs on 10 aircraft with high flying-hour requirements compared to the rest of the fleet, as well as addressing known structural issues. The repairs will be completed in a 30-day flow under a fly-in, fly-out program with 5,000 hours of repair invested into each plane.
Phase one of structure repairs will be split between two shifts and will have sheet metal and aircraft technicians tackle the workload. Phase two, which will involve a steady stream of B-1s coming through each year for repair, with 14,000 hours of repair planned per airplane, will begin next month. More than 100 people have been hired in the past year in preparation for the workload, which should last for the duration of the B-1’s life.
“We’ve flown it hard, worked it hard and now it’s time for repairs so we can have the aircraft ready to deploy when necessary to support the needs of the nation,” says Barnes.
Photo: USAF/R. Nial Bradshaw
The existing supply system “could not meet the demand requirements for these cowlings,” says Colonel Robert Nash, Georgia Air National Guard, 116th Maintenance Group commander.


“The whole machine is adjustable; it’s pretty ingenious,” says Staff Sgt. Quinn Smith, a 116th Aircraft Structural Maintenance Section sheet metal technician.
Section airmen turned to the Aircraft Metals Technology Section to explain what they wanted. The table was designed and built in a week for only $400.
Photo: USAF/David Owsianka
The maintenance technicians expect to improve the table design further over time.
“The mentality these maintainers have is that no matter what their circumstances are, they are going to figure out how to make it, build it or otherwise produce it,” according to Nash.
Photo: USAF/Kelly White
“Most maintenance people replace parts. We have to make our own parts from raw materials and then install them,” says Master Sgt. Andrew Liederbach, a 386th Expeditionary Maintenance Squadron combat metals flight chief.
In a deployed environment, crews are responsible for anything and everything fabrication. Whether it’s assembling parts or creating them from scratch, the combat metals flight crew supports units stationed with the 386th Air Expeditionary Wing and those passing through.
In a recent mishap, a bird strike punched a softball-size hole in the leading edge of a wing on a C-130 Hercules.. Liederbach and his team fitted the aircraft with a one-time flight patch so it could return to base for full repairs.
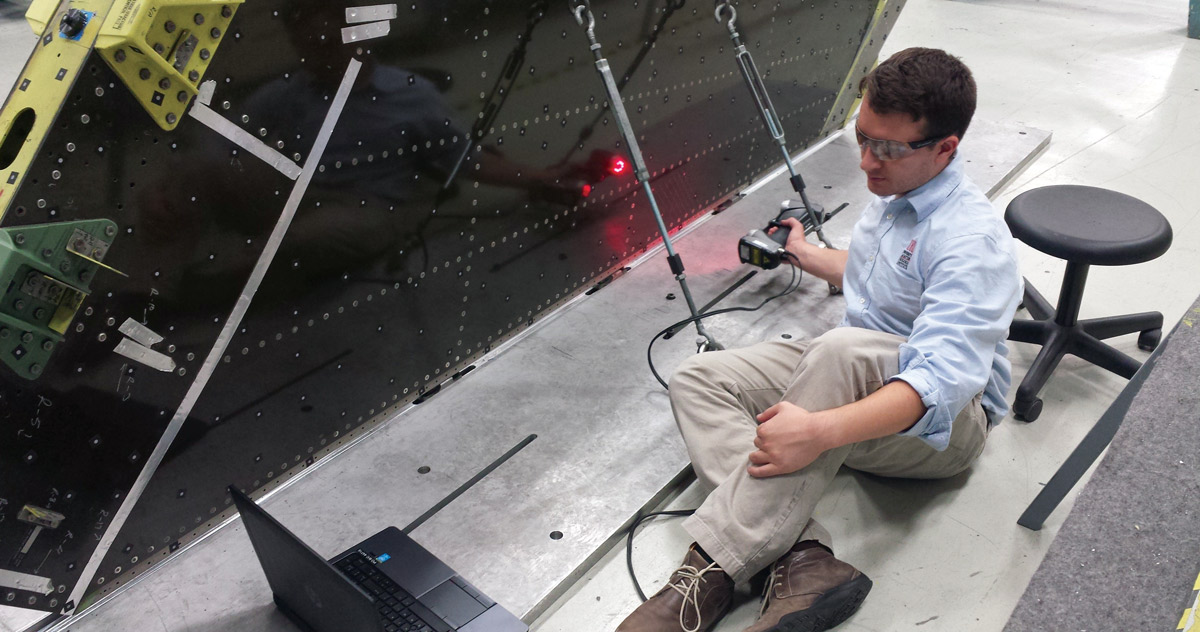
Photo: USAF
His team spent 144 hours creating more than 30 parts from scratch, including a new rib support. This eliminated nearly three weeks from the downtime of the aircraft.
“We would have potentially lost the ability to fly at least four missions,” notes Chief Master Sgt. Bryan Ford, 386th Expeditionary Maintenance Squadron superintendent.
This fabrication work is mission critical and the airmen, maintenance staffs and sheet metal workers are an asset the U.S. Air Force could not exist without.