lexible factory setups allow manufacturers to use automation to create a fully connected, smart production line. According to research from Deloitte Insights, “Smart factories go beyond simple automation. The smart factory is a flexible system that can self-optimize performance across a broader network; self-adapt to, and learn from, new conditions in real or near-real time; and autonomously run entire production processes.”
“Automation and autonomous processes have been a major growth point in the industry for several years,” says Ryan Welcome, who works for machinery manufacturer Trumpf Inc. as a TruConnect specialist for the TruLaser Center 7030. Companies are taking a “deeper look into total throughput of processing sheet metal parts,” he notes. “To really evaluate the process chain, we need to look at more than just linear cutting times.”
Trumpf developed the TruLaser Center 7030 in response to the need for a machine capable of taking away common pain points with reliable, repeatable processes. The TruLaser Center 7030’s LoadMaster separates and loads the sheet onto the table—ready for cutting. Once the part is cut, it is clamped and guided out of the skeleton using SmartLift pins and small suction cups and moved to the sorting area parallel to production. The scrap skeleton is sent to a disposal area parallel to sheet loading. Thanks to these technologies, the laser center can even cut and handle very small and delicate parts without damaging them.
Welcome says the main benefit of this machine is that Trumpf went back to the drawing board to create an ultimate sorting solution. “For example, we wanted to remove the support slats from the equation. Slats allow smaller parts to tilt, unless they are micro-jointed/tabbed to keep the geometries in place for transport. With a sorting laser, you can’t pick parts that are tabbed, so you have no choice other than to remove the slats from the equation or massively limit yourself to parts that must span several slats so that tilting doesn’t occur.”


To offer the broadest possible size range of parts being processed, Trumpf developed the SmartGate, “a system with two copper plates that move parallel with the cutting head in the X axis to support the geometries during cutting and removal,” Welcome explains. “Then we move the sheet over brush support tables in the Y axis via a clamping rail. Finally, we have an additional superimposed Y2 axis in the cutting head. These combined movements offer the highest possible dynamics in laser cutting.”
Because there are no slats, typical problems like backburn marks from the beam cutting over the slats, or reheated spatter on the slat tines adhering to finished parts, are eliminated—along with the subsequent post-processing sanding and cleaning. “Also, the customer doesn’t need to stop the machine for slat cleaning or replacement of the loading pallets.”
After developing this new method for stabilizing parts during the cutting process, Welcome says Trumpf’s next goal was to continue the stability during part removal. “Parts ranging from 1.18 inch by 1.18 inch to 6.25 inch by 6.25 inch are clamped between a head-mounted ejection cylinder and the SmartGate, then are lowered and released under the sheet into eight possible bin locations inside the machine. Alternately, parts ranging from the size of a business card to 78 ¾ inches by 59 inches can be palletized onto a storage unload tray or common pallets with our SortMaster Speed pneumatic suction arms, which can hold and transport parts weighing up to 264 pounds.”
For some customers, the TruLaser Center 7030’s capabilities will provide the “ultimate solution for all their cutting needs, but we consider it to be an addition to our line of 2D cutting technologies and not a total replacement,” says Welcome. He notes that the TruLaser Center 7030 would be ideal for any company “interested in producing high-quality parts with limited operator intervention and post-processing.” In other words, only “one-third of an operator” is needed to support raw material loading, scrap maintenance and bringing finished parts downstream.
“Post-cutting breakout stations with lots of manpower for separating parts, removing scrap skeletons and performing secondary operations—such as grinding tab marks away or sanding other imperfections—are largely unaccounted for as part of the total process,” Welcome says.
“The goal of the TruLaser Center 7030 is to have maximum throughput with minimal intervention, having sorted stacked parts of optimal quality ready for shipping or sending downstream to a bending cell or other operation.
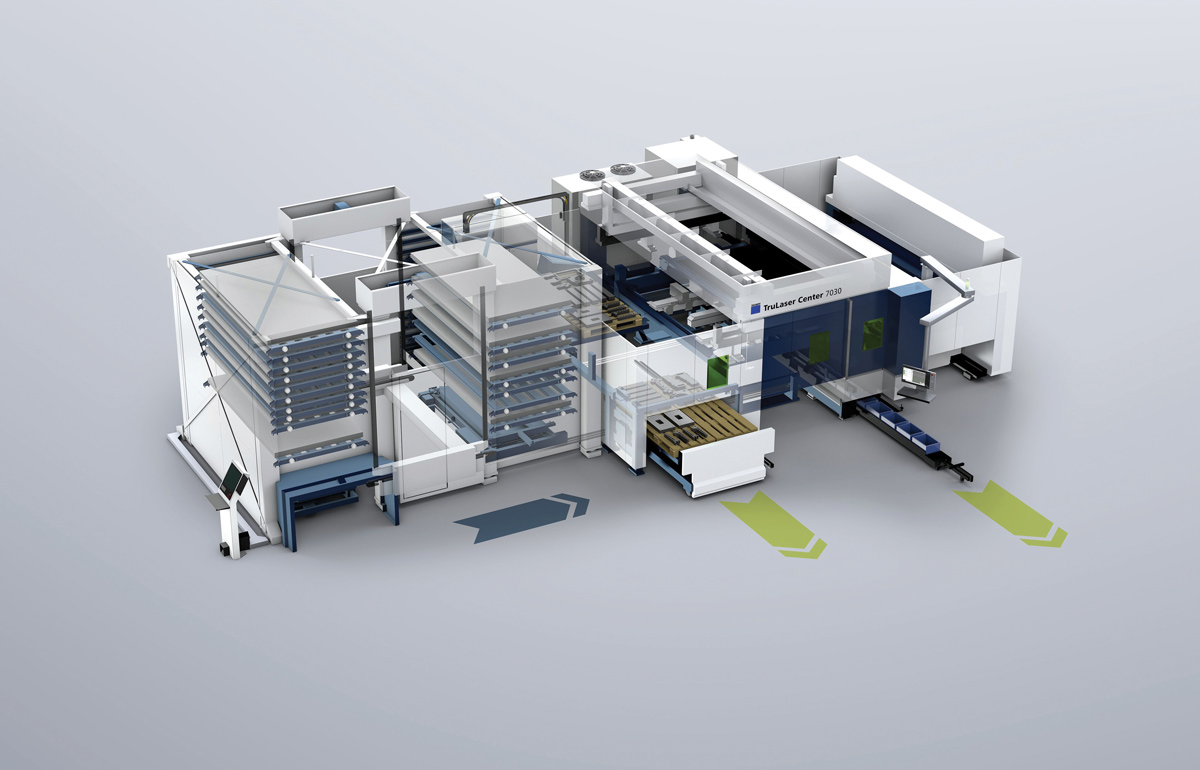
“Ideally, the part never gets touched by a human hand until welding, painting or assembly is needed,” he continues. “My experience with customers in the sheet metal industry shows that they have plenty of ways to re-utilize this labor.”
Apart from increasing productivity, a sorting machine contributes to lower injury rates among employees handling the parts. “Also, we wanted to build a machine that would run lights-out during unmanned shifts throughout the week and weekend,” says Welcome.
A flexible machine can address a variety of different needs—from manpower issues to tackling large, cumbersome parts that are difficult to move. Welcome says that the TruLaser Center 7030 “can be configured with our standalone storage towers or larger, scalable modular systems. Whether the goal is feeding raw material to the machine for processing, storing or removal of finished parts or providing a bending cell with cut blanks, all needs can be addressed.”
Furthermore, all these functions “can occur parallel to a material handler loading raw sheets into the automation system. The thought here is to always have the machine producing with other processes occurring harmoniously.”